Fully automated counter pressure bottle filler and capper for beer and other carbonated beverages.
Key Features:
- Handles nearly every size beverage bottle that uses crown caps
- Foam free counter pressure filling of carbonated beverages
- Automated cap feeder and capper
- Automated bottle sanitizing prior to fill
- Small footprint - Low product waste
- Very low cost relative to other systems available
- Perfect for start-up nano and micro breweries
The Fill-Boss Pro uses counter pressure fill technology. This means that the bottle is pressurized to the same pressure as the beverage tank (keg or brite tank) prior to filling. Typically the bottle is purged of oxygen (air) by filling it first with CO2 until all the air is forced out. CO2 is heavier than air so when introduced to the bottle, the CO2 settles to the bottom. After the air is purged, the bottle is pressurized with CO2 until the pressure reaches the same pressure as the beverage keg or brite tank. Flow of beverage is then allowed to flow into the bottle and pressure is gradually released from the bottle allowing the CO2 to escape and beverage to replace it. This process of filling under pressure reduces foaming greatly.
The filler is completely adjustable, allowing it to fill nearly any crown cap type bottle. The innovative fill head design on the Fill-Boss Pro dispenses the beverage along the inside walls of the bottle, further preventing foaming and increasing flow rates of beverage.
One of the KISS features of the Fill-Boss Pro is the ability to invert the bottles beneath the indexing conveyor. This was made possible by an innovative linkage mechanism that clamps the bottles, regardless of the diameter, exactly in the center of the conveyor link. This is required to assure alignment with the fill head, capper, and sanitizer. This bottle clamp design automatically releases at the load/unload position allowing the user to easily remove filled bottles and replace them with an empty bottle. When the conveyor indexes, the bottle is automatically clamped and eventually conveyed to the underside of the conveyor.
The prototype also does not show the automated sanitizing feature of the machine. The computer models shown below show the unique dual tray feature that allows us to sanitize the bottles automatically as they are inverted under the conveyor. The lower tray is filled with sanitizing solution. When the inverted bottles pause above the sanitizing positions, the high pressure pump forces a jet of sanitizer into the bottle(s). The upper tray captures any drips coming from the filler itself and keeps contaminants out of the sanitizer.
We've spent considerable time developing a cap feeder that we have not shown in this video as it is so unique, we don't want to risk others copying the design before we get this to market! The prototype shows the magnetic capping head, but as the prototype was designed to test the reliability of the system, we excluded showing the actual capping as the bottles are simply emptied when they get inverted and filled again when they are presented to the filler. That allowed us to stress test the system without the need to remove caps.
We've found the maximum fill rate to be about 120 bottles per hour per fill head, so the 2 head would be 240 bottles/hr and the 4 head 480 bottles/hr. This is the maximum rate and should only be expected for non-carbonated beverages or low foam beverages. The fill rate is decreased for beverages that foam considerably as the bottles must be filled slower.
Single Fill Head Design
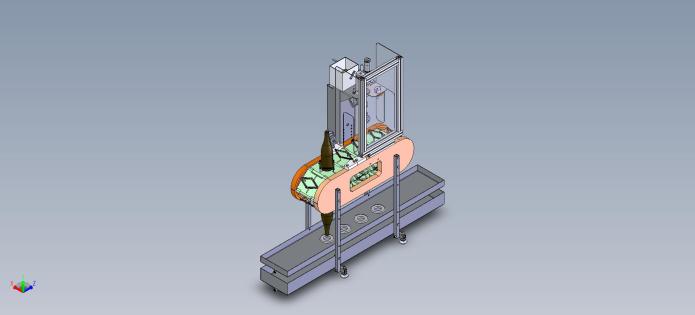
Dual Fill Head Design
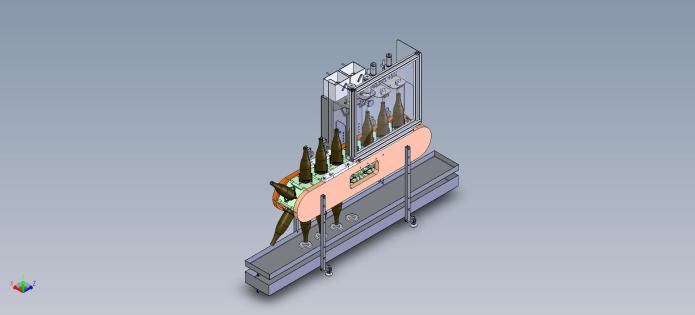
4 Fill Head Design
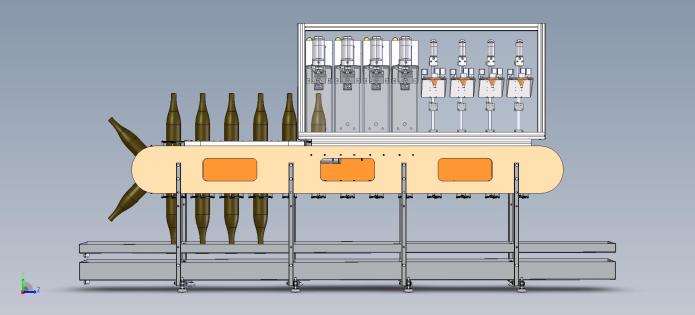
Your Beer, Your Way!! Brew like a Boss!
#nanobrew, #fillboss, #automatedbottlefillerandcapper, #counterpressurebottlefiller,